Intelligent
Energy Management
Battery
management systems are answering the critical global need
for safer forms of energy and large-scale renewable energy
storage Words: Steve Tartaglia In the year 2013, advanced
battery systems are used frequently throughout the marine
industry. Lithium ion cells are up to four times more
energy-dense than lead-acid batteries, and a battery management
system (BMS) is required to protect the cells and maintain
safety. But, are yacht owners knowledgeable of the BMS
and the decisions it is programmed to make?
Figure 1: The Lithionics Battery NeverDie marine BMS is
systems-compatible today
In
the previous issue of Electric & Hybrid Marine Technology
International, an approach to a modular lithium ion battery
system with an external BMS for both expandability and
emergency-bypass was discussed. Most lithium batteries
have an internal BMS that is not accessible or serviceable.
Another major advantage of the external-type BMS is the
ability to upgrade it in order to expand its capabilities
to manage additional marine systems in the future.
Can
a lithium ion battery with a BMS successfully integrate
into existing marine environments? The answer is yes,
provided that the battery manufacturer properly understands
all the marine systems that are connected to that battery
system. What are the pitfalls and what are the solutions?
As
depicted in Figure 2 (below), a
BMS has high voltage cut-off (HVC) with cell balancing
called shunting (shown in the bottom graph) and low voltage
cut-off (LVC) (shown in the top graph).
Figure 2
The BMS keeps the system operating in the usable power
zone but existing marine systems can trigger HVC or LVC
disconnects, with harmful results to the systems. HVC
occurs if overcharging is sensed, or, if during cell balancing
at the end of the charging cycle, excessive top-end shunt
balancing is occurring. This can and will happen because
the yacht is likely using multiple charging sources, such
as solar charge controllers, alternators, diesel generators,
and inverter-converter chargers that are designed for
lead-acid batteries. The BMS will temporarily disconnect
power to the terminals. However, this also shuts off the
power flow. So, what are the solutions?
Dual-channel
BMS
First, BMS programming points for HVC, shunting and LVC
should follow the lead-acid charging algorithms already
embedded in the existing charging sources. Lithionics
Battery decided two years ago to offer a BMS that follows
the GEL settings for charging. However, transformer-based
chargers lack accuracy in many cases, and HVC can occur.
Therefore, a dual-channel BMS has been developed by Lithionics
Battery. Basically two BMS units in one, one pathway is
for charging currents and a separate pathway is for discharge
currents. It is fault-tolerant, which permits HVC to trip
and disconnect the incoming charge current without disconnecting
the power flow. For example, a yacht entering a harbor
is being solar charged. A charging voltage spike occurs,
HVC is tripped, and the yachtsman is now without power
to the ship's navigation systems. Fortunately, the Dual-Channel
NeverDie BMS can solve that particular problem.
A
Dual-Channel BMS is capable of independently controlling
charging and discharging currents:
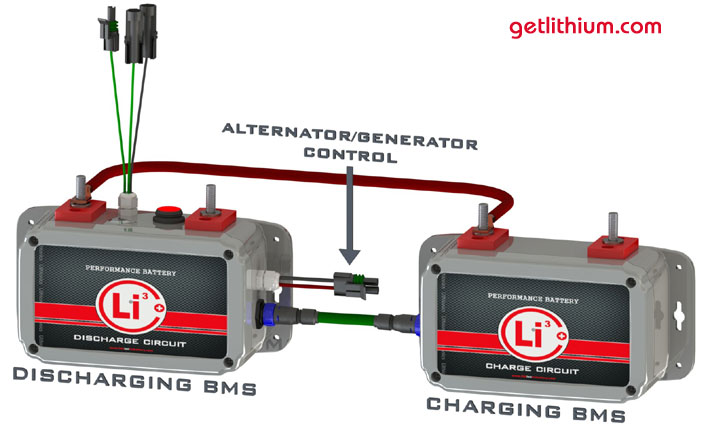
Alternator
charging controls
Numerous news stories have been published detailing alternator
fires caused by lithium-ion battery shutdown. If a BMS
detects overcharging from an alternator, it will trip
HVC to protect itself. But the power has to go somewhere,
and the alternator is forced to absorb the energy and
self-destruct. The solution is a field effect control
(FEC) module on the BMS. It is a special circuit that,
when connected to the alternator, an HVC prealarm signal
will first switch off the field wire on the alternator
to avoid tripping HVC. It may not be a failing alternator,
but perhaps an older alternator that lacks Voltage accuracy.
The FEC NeverDie BMS is therefore fault-tolerant of the
alternator and protects both the battery and the alternator.
(NOTE: we now call the alternator "FEC" BMS
option "FCC" for Field Control Circuit.
For example, a yacht installation has four alternators
on a single serpentine belt drive. One alternator controls
the diesel propulsion engine and the other three alternators
are charging a large lithium-ion battery bank that in
turn provides power to the entire yacht including inverters
and air conditioning systems. One alternator begins to
fail and is sending in bad voltage or unrectified current.
The BMS will simply switch off the field wire on that
alternator, preventing alternator over-heating (free-wheeling)
and allowing the other alternators to continue. No HVC
is tripped and the entire system stays up and running
until the alternator is serviced.
BMS
with digital and analog interface outputs and controls
Most lithium-ion battery systems communicate to peripheral
hardware by CANbus digital signal processing. Marine systems
today are simply not CANbus compatible. To integrate safely
and easily, a BMS should offer a range of digital and
analog outputs that are compatible with existing marine
systems. The outputs need to be serial data, bluetooth,
0-5V, or other formats. The BMS provides communications
and control signals that allow the BMS to not only communicate
with but also control other marine systems. The FEC NeverDie
BMS is not independent of the installed marine systems,
but, instead, interdependent.
For
example, a yacht is using a Fischer Panda DC diesel generator
to charge the house or propulsion battery bank. Fischer
Panda engineers provided support to Lithionics Battery
to create a generator charge-enabled interface. This allows
the NeverDie BMS to start the generator when charging
is required and turn off the generator when the battery
is fully charged.
Battery
power reserves
A lithium battery BMS has a single Low Voltage Disconnect
point (LVC). But, like the last dollar from a paycheck,
it never comes at the right time. The NeverDie Power Reserve
system offers a dual LVC system.
An
example of this in use includes batteries that are both
deep cycle and engine starting. The ideal marine battery
would be able to both deep cycle and be capable of engine
starting. A 250HP outboard engine normally has two Group
31 AGM batteries at 150 lb (68.1kg). A professional bass
fisherman in competition will isolate one battery for
engine starting; and the other battery for deep cycling
to support GPS, fish-finders and live-wells for his prized
catch. A single 30 lb (13.6kg) lithium battery can replace
two batteries if it has a power reserve feature. The battery
will provide deep cycle power for all-day electronics
use, and the dual LVC power reserve ensures the single
battery has enough cranking power at the end of the day.
For example, a boat using a lithium ion battery powers
an electric outboard motor. Returning home, the battery
runs out of power within sight of the dock.
A dual LVC BMS provides a 10% power reserve system offering
emergency power. For example, a yacht maker offers a master
power switch connected to the BMS. A single switch turns
off all systems and protects the battery from discharge
when leaving the boat. But what about the bilge pumps?
The dual channel LVC system turns off the mains and all
parasitic draws, but the second LVC channel permits power
to the bilge pumps down to 97% depth of discharge. If
necessary, should an emergency arise, all the battery
power in the lithionics battery is diverted to the bilge
pumps. The dual LVC retains enough energy to restart the
engines or generators.
Looking ahead
Lithium ion batteries provide huge gains in weight savings
and energy density, and support modern systems such as
DC-powered air-conditioning systems. Customers also report
that there is a real return on investment when using these
batteries. However, investment in a lithium battery only
makes sense if it allows the boat owner to use the existing
systems. The gains are also lost if the battery causes
another component to fail. Lithionics Battery's aim with
the NeverDie BMS is to ensure that the performance improvements
and cost savings stay in the yacht owner's pocket. So,
it has to be safe, and it also has to be easy.
Words:
Steve Tartaglia
NOTE:
When connecting an Inverter-Charger with a single set
of DC power cables to the Dual Channel BMS, we generally
recommend that you connect its positive DC power cable
to the Dual Cahnnel BMS box's "LOAD" terminal.
This applies to reliable inverter-chargers like Victron,
Xantrex and some other good quality brands.
|